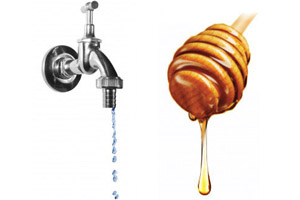
The fluid viscosity is defined as the leakage resistance, i.e. The more viscous the medium, the less leakage.
However, a more viscous liquid affects the performance of the pump in several ways:
- decreases the pump power (kW);
- reduces the head and volume of the pumped liquid;
- there are problems with the mechanical seal due to the problems of the shaft movement and the shifting of the stuffing box packing;
- bearings are subjected to a higher radial load when the pump shaft is displaced;
- pumped liquid will not be able to lubricate the ground surfaces if the thickness of the liquid film is less than 0.000040 microns.
Viscosity is a measure of the density of a liquid. Soot and motor oil are thick or highly viscous liquids. Petrol and water are less dense, liquids with low viscosity. Do not confuse the viscosity with the specific gravity of the same fluid. The specific gravity is a measure of the weight of the liquid compared to an equal volume of fresh water of 20°C.
Motor oil has a low specific gravity (it floats on the surface of water), but has a high viscosity of more than 500 cSt (centistoke is a unit of kinematic viscosity). Mercury has a high specific gravity (13.7), but a low viscosity, only 0.118 cSt.
It is important to note once again that these two properties of the liquid are completely independent of each other.
The viscosity of a liquid can vary markedly with the temperature of the liquid, but it rarely changes with a change in pressure. It has long been known that hot oil is more liquid than cold, so before determining the viscosity of the liquid, you should first measure its temperature. Without this information, you can purchase an inappropriate pump.
Temperature is not the only parameter that you should pay attention to when you check the fluid for viscosity.
There are four classes of liquids that change their viscosity with mixing, and one that does not change its properties:
- linear-viscous (Newtonian) liquids are independent of the amplitude and type of motion to which they are exposed. Typical for this class of liquid - mineral oil and water;
- dilatant (viscosity increases with increasing shear rate) liquids increase viscosity with mixing, some of these liquids can become almost solid inside the pump or pipeline. Everyone knows that with mixing, the cream turns into butter. Confectionery mixtures, clay masses and other highly filled liquids do the same.
- plastic fluid has a yield strength that must be exceeded before the flow begins. From this point on, the viscosity will decrease as the stirring occurs. Tomato ketchup is the best example of such a liquid;
- pseudoplastic liquid shows a decrease in viscosity with increasing mixing, but it does not have a yield point, many emulsions fall into this category;
- thixotrophic fluids exhibit a decreasing viscosity with increasing agitation, but the viscosity, at any particular speed, may depend on the previous mixing of the liquid. Examples of a thixotrophic liquid are: glue, non-droplet paint, lubricant, cellulose compounds, soap, starches and resin.
There is dynamic viscosity and kinematic.
Consider the dynamic (absolute) viscosity:
- in the international system of units (SI), the dynamic viscosity is measured in Pascal - seconds (Pa•s);
- there are extrasystem values of dynamic viscosity measurement - "poise" (P) and its derivative "centipoise" (cP);
- water, at a temperature of 20.2°C, has an absolute viscosity of 1 centipoise;
Let us consider the kinematic viscosity:
- basic unit of measurement in the system of units (SI) - m² / s,
- the common unit of measurement in the CGS (centimeter-gram-second) "Stokes" and its derivative "centistoke" (cSt);
- extra-system unit - Engler's degree;
These types of viscosity are interrelated as follows:
Kinematic viscosity = absolute viscosity / specific gravity.
Absolute viscosity = kinematic viscosity * density.
Since the specific gravity of water at 20°C is practically the same, the kinematic viscosity of water at 20°C for all practical purposes is therefore 1.0 centistokes.
Temperature, °C | η, 10-6 Pa*s |
0 | 1797 |
10 | 1307 |
20 | 1004 |
30 | 803 |
40 | 655 |
50 | 551 |
60 | 470 |
70 | 407 |
80 | 357 |
90 | 317 |
100 | 284 |
110 | 256 |
120 | 232 |
130 | 212 |
140 | 196 |
150 | 184 |
Unfortunately, there is no acceptable analytical method for predicting pump performance when the viscosity of a liquid differs from the viscosity of water. Many tests were carried out and the data were compiled in the form of diagrams and nomograms, as a result, the efficiency of the pump can be correctly estimated, for liquids of almost any viscosity.
The importance of measuring viscosity in the food industry.
High quality food is very important for consumers. In this industrial sector, the production of products that meet the high demands of consumers is a challenge for quality control specialists. Control studies should be fast, accurate and not too expensive. This particularly applies to physical measuring variables, such as viscosity.
The viscosity of a liquid plays an important role, almost at all stages of production in the food industry. Many liquid media must be carefully piped. In the production process, the aggregate state of the food product may vary, from liquid to pasty state.
Name of liquid | Temperature, °C | Viscosity, mPa*s |
Water | 20 | 1 |
Alcohol | 20 | 1,2 |
Milk | 20 | 3 |
Juice | 20 | 55-75 |
Honey | 40 | 2.500 |
Fruit concentrates | 20 | 1.600 |
Jam | 20 | 8.500 |
Glucose | 35 | 20.000 |
Vegetable oil | 20 | 2.000 |
Chocolate | 50 | 17.000 |
Ketchup | 20 | 1.500 |
Yogurt | 40 | 152 |
Tomato paste | 20 | 4.000 |
Feed molasses | 30 | 100.000 |
Glycerol | 20 | 1.500 |
In the food industry, various types of sugar, such as glucose syrup, are often used to sweeten food and beverages. Many types of syrup are obtained from the enzymatic degradation of starch and are an important component in the starch industry. Because syrups are sticky, they are often used as binders in the manufacture of food products, such as chocolate flakes or sauces. Viscosity and rheological property (flowability), depend on the adhesive properties of the starch contained in the liquid. Starch has different characteristics, depending on the temperature and the environment. For example, an increase in temperature, has a hardening (thickening) effect. However, when cooking, starch has a liquefying effect. When the liquid cools down again, the starch again thickens it. This state is characterized by viscosity. Even for soups, the correct consistency is achieved by adding thickeners. When determining the yield sauces, honey, mayonnaise and other liquid additives, for quality control of the important role played by the temperature-dependent viscosity.
In the process of quality control of incoming fluid, viscosity is an important control variable when it comes to differentiating different qualities of raw materials and eliminating problems in their further processing. Depending on the composition, selective measurements can be made in the laboratory, but in some cases, it is necessary to carry out measurements on site or directly in the production process. The received data are stored and sent to specialists for further processing.
Rapid and simple determination of viscosity is very important for quality control, manufacturing process and pumping viscous liquids.
Influence of the viscosity of the pumped medium on the pump.
When viscosity and other operating parameters are known, it is possible to proceed with the selection of pumping equipment. In most cases, a centrifugal pump is suitable for liquids with low viscosity, since their pumping creates a high fluid shear. As the viscosity increases, the performance of the pump must be adjusted to take into account the additional shear resistance.
In general, forced displacement pumps are the best choice when working with viscous fluids. They tend to operate at lower speeds and transmit fluids with less shear energy than the centrifugal pump. There are many pumps with forced displacement, which can be selected based on the requirements for the pumped medium.
Viscosity is an important factor in determining the frictional losses due to the shear energy in the liquid process system, as well as in the selection and calibration of valves, filters, instruments and pipelines. There are many available reference materials that provide data on friction losses for a given flow rate, tube size and fluid viscosity. There are also data that convert pipe fittings and valves into an equivalent straight pipe length.
Types of food pumps for pumping viscous liquids.
Diaphragm pump.
This pump is suitable for pumping liquids with a viscosity of up to 20,000 cSt. These pumps, when pumping liquids with high viscosity, have low efficiency, are not suitable for liquids having a low-flow and non-flowing structure. Can provide capacity up to 72 m3/h, pressure up to 8.5 bar and self-suction up to 8 meters.
Peristaltic pump.
The peristaltic (hose) pump, like the membrane type pump, is not suitable for pumping liquids with high viscosity, since the limitations range from 20,000 to 70,000 cSt. This pump has a number of advantages compared to other pumps, such as: the most delicate pumping of liquids, the absence of liquid contact with the pump body parts, the high degree of self-suction to "dry", can provide pressure up to 15 bar and productivity up to 60 m/self-priming up to 8.5 meters.
Screw pump.
The pump is capable of pumping liquids with a viscosity of up to 1 million cSt, provides an operating pressure of up to 32 bar, and a capacity of up to 320 m3 another advantage of screw pumps is the pumping of liquids with the content of solid particles.
Rotary pump.
It is capable of pumping liquids with a viscosity of up to 1 million cSt, provides a pressure of up to 30 bar and a capacity of up to 160 m3.
When working with viscous liquids, only practical experience of pump operation will help to determine how the liquid will behave. The information obtained in combination with the available viscosity data of the pumped liquid (viscosity table) will allow an adequate analysis of the characteristics of the fluid system. After the fluid processing system has been developed and the pump operating parameters determined, it is possible to select the appropriate (suitable) pump.
The specialists of AvtokomTehnolodgy group of companies are ready to pick up for you pumping equipment for technical parameters and characteristics of the pumped medium. We also make selection of mechanical seals for pumps based on the conditions of their operation. Our mechanical seals are qualitative analogues of the original mechanical seals pre-installed in pumps, and in most cases exceed them in terms of service life.