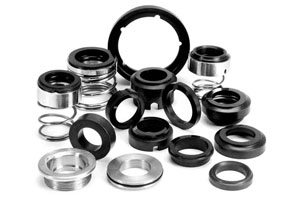
General information.
As it is, mechanical seals are among the most common and needed kinds of sealing elements used in machinery. This kind of seals is widely used in pumps, compressors, agitators, chemical production process equipment, food, pharmaceutical, petrochemical, metallurgical and energy industries. In the chemical industry, for example, mechanical seals can play a key, and even, leading role. You can see an example of a mechanical seal in Image 1.
Image 1. Mechanical seal.
The specific design feature of the mechanical seal is that when two parts are pressed together tightly along the end planes (a stationary part and a rotating one), complete leakproofness can be achieved. The friction couple, which acts as the main sealing element, is produced from special materials having a high quality of friction end surface finishing, which ensures its maximum leakproofness. This type of seal is used for sealing fast-rotating shaft machines, such as shafts of pumps, various chemical equipment, compressors, agitators, reactors, etc. The reason for using this type of sealing in such equipment is that seals of other types do not provide secure leakproof conditions and they are less efficient, particularly in sealing poisonous and aggressive media.
Reference:
To seal housing and shaft units and plants, packing glands were conventionally used (Image 2).

Image 2. Packing gland unit and its design.
Although the packing gland unit has a simple design, it also has a number of disadvantages:
- the gland packing service life decreases if the gland is used in corrosive media;
- either the shaft jacket or the shaft itself is subject to wear (depending on the design);
- high friction (due to the constant high-speed rotation of the shaft, there is a higher level of friction,wich causes the packing gland unit to heat, and this results in even greater friction. It is possible to decrease heating by reducing the packing gland temperature, for example, by using a special cooling system (which will lead to a higher cost of the unit), or a sealed medium can be used (but this option is unacceptable in case of pumping corrosive or poisonous media);
- it is necessary to replace the packing and tighten the packing gland very frequently, which leads to extra production equipment maintenance costs and, consequently, decreased performance of the entire process flow.
All these downsides are non-existent in mechanical seals, and although their design is more sophisticated and the sealing unit is more expensive, the use of mechanical seals is more often than not justified.
Mechanical seal design.
Image 3 shows a mechanical seal design.
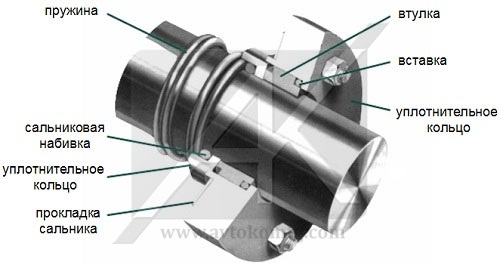
Image 3. The simplest mechanical seal.
In Image 3, you can graphically see three loop seals, two of which are auxiliary. The first loop is a stationary ring seal of the mechanical seal, which is rigidly fixed in the housing and is made from round or square section packing or gasket. The second is a moving ring seal of the mechanical seal and is able to move progressively (driven by the spring), parallel to the shaft axis, which creates pressure on the stationary ring required for sealing. The above seal is also made from sealing rings, cup seals and packing, as only small axial movements occur in the shaft-moving sealing ring couple. The third loop is the mechanical seal itself, where leakproofness is ensured by means of a tight contact of the moving and fixed ring end surfaces. In this junction, leakproofness is achievable in practice only if the best possible mating surface finishing quality is obtained. Irregularities as small as 1 mcm can disrupt normal operation of the mechanical seal. The friction surfaces have to be subjected to lapping and polishing (to ensure a high level of finish), and they can be spherical, flat and tapered. Flat surfaces are generally used, since it is easier to obtain good surface finish during the finishing operation, in which case the width of the friction ring surface shall not exceed 6-8 mm, and one of the surfaces is made from a more wearproof material. In manufacturing friction couples, different grades of carbon (graphitized carbon) materials, steel, hard alloys (tungsten carbide), cast iron, as well as ceramics and polymers, are used. Friction couples are selected on the basis of the seal operating conditions.
Reference:
A list of the most common materials used for making friction couples can be found below, in tables 1-3.
Table №1. Corrosion-resistant metals and alloys:
Table №2. Facing materials:
Table №3. Non-metallic materials:
Table №3. Non-metallic materials(supplement):
Mechanical seal types and designs.
Different types of mechanical seals are used depending on the operating conditions.
1. Single mechanical seal.
If the equipment operates in non-toxic and chemically neutral liquids, where the operating medium tempreature does not exceed 200°С, and the pressure is not more than 20 MPa, single mechanical seals are used. External single mechanical seals are used for abrasive media, whereas internal ones are intended for media with lubricating properties. This type of seal is shown in Image 4. It can be supplied with additional cooling units to increase efficiency.

Image 4. Single mechanical seal.
2. Double mechanical seal.
Double mechanical seals are used in equipment which operates to pump liquified gases, oil products and media containing toxic and harmful substances, as well as abrasive inclusions, where the operating medium temperature is not higher than 400°С, and the pressure is not in excess of 30 MPa.
The design variations of double mechanical seals are:
- "face-to-face" seal;
- "back-to-back" seal (Image 5);
- tandem seal (Image 6).
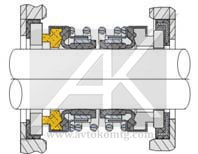
Image 5. Double back-to-back mechanical seal.
This type of seal can be equipped with 'cleaning' units, which allow minimizing abrasive wear, cooling units, and backpressure units, which supply 'locking' liquid between the sealing loops to prevent the operating fluid from leaking.
Double mechanical seals can be supplied with additional units:
- standalone, e.g. with an impeller (which provides liquid circulation or pressure);
- external, with fittings to connect external units.
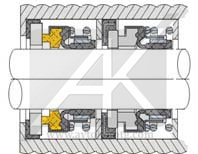
Image 6. Tandem mechanical seal.
3. Cartridge type seal.
One of the most popular types of mechanical seals is the cartridge seal. In this type of seal, both parts are made as a single module or unit designed for specific stuffing box standard sizes as per DIN, API, ISO, etc.
This type of seals is produced for specific operating conditions and kinds of equipment.
An example of a single cartridge seal is shown in Image 7.
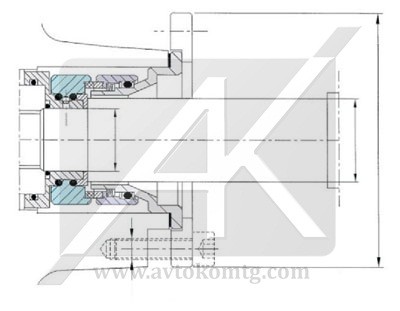
Image 7. Single cartridge seal.
Image 8 shows a double cartridge seal.
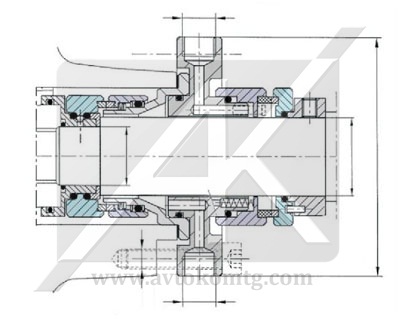
Image 8. Double cartridge seal.
Apart from one or several loops, seals may have additional cooling, backpressure, heating, and lubricating units, different sensors, flushing units, etc. Commercially produced cartridge type seals can be used at temperatures of up to 650°С and a pressure of up to 80 MPa depending on the materials and design used.
4. Gas mechanical seal (dry-running gas seal).
This type of seal has been in use since the mid-1980s. The operating principle is based on creating a thin gas layer of about 2-5 mcm between the sealing rings, which occurs due to the presence of special "V" or "U"-shaped pockets, whose thickness is comparable to the thickness of the end clearance, and which are located on the sliding surface of one of the rings running from the middle of the ring to its outer edge from the shut-off gas side. The rotation of the ring results in the shut-off gas being supplied into the pocket space, which leads to a clearance being created and, consequently, to contact-free gas sliding, which keeps friction and seal wear losses to a minimum. The process air or nitrogen used for the purpose has a pressure which is 5 to 10 % higher than the operating fluid pressure. This type of seal is ideal for operation at low temperatures, with low-temperature boiling liquids, ensuring production process cleanliness and making any leakage absolutely impossible.
You can see an example of a dry gas seal in Image 9.
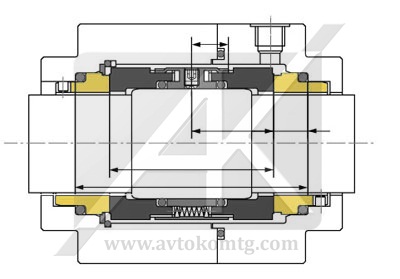
Image 9. Dry gas seal.
A disadvantage of this kind of seal is its high cost and design complexity.
5. Magnetic fluid seal.
In magnetic fluid seals, the role of a sealing element is performed by magnetic fluid, which is kept in the clearance between the shaft and the housing by means of a permanent magnet. This type of seal does not require maintenance and operates with some minor leakage. The seal does not wear down because the sealing element is a liquid, which means there is no friction between the rotating and stationary parts. As a result, the service life and interrepair cycles of magnetic fluid seals are quite considerable, and the friction torque is consequently low. This kind of seal gives no trouble when operating in ultrahigh vacuum, at tens of thousands of rpm, at pressures up to a few atmospheres and rather high temperatures.
You can see an example of this kind of seal in Image 10.
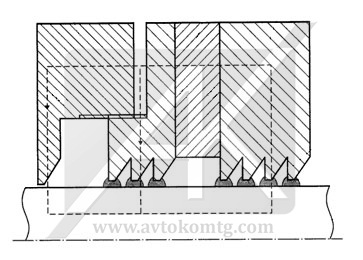
Image 10. Magnetic fluid seal.
The most common application of the magnetic fluid seal is rotary sealing of vacuum process equipment. This type of seal is mostly used in cosmetology, biotechnology and pharmaceutics. Reliability and best leakproofness levels are important for processes with high sterility requirements, which makes magnetic fluid seals most attractive and popular in this application. However, magnetic fluid seals cannot be used at high differential pressures, and this is likely to be one of the disadvantages of this kind of seal.
Our specialists will select matching mechanical seals or analog of mechanical seal for pump in the catalog.