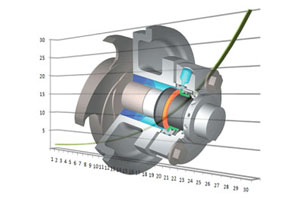
Coefficient of load:
For assessment of mechanical seal except coefficient of hydraulic unloading use also dimensionless coefficient of loading x.
For large differences sealing pressure ratio hydraulic unloading and load factor are almost identical. Dynamic friction auxiliary seals pr generally not taken into account.
Sliding pressure:
By the term "sliding pressure" means the contact pressure on the sliding surfaces remaining after equilibration of all active forces on the sealing surface of the hydraulic pressure. Sliding pressure pG depends on pressure difference, coefficient of hydraulic unloading, a ratio of pressure in a sealing gap (pressure gradient indicator and spring pressure. Depending on the shape of the two sealing surfaces and thus forms a sealing gap, the pressure gradient indicator k1 can range from 0 to 1.
For seals with a sealing gap narrowing in the leakage direction (V-shaped gap) when loading external pressure indicator k1 can take values greater than 0,5, and for sealing with a sealing gap widening in the leakage direction (A-shaped gap) when loading an external pressure indicator k1 can be set to less than 0,5. To simplify the calculations are commonly used value of k1 = 0,5. Pressure slip under adverse conditions may take a negative value, which leads to the sealing surfaces of the joint disclosed and hence to excessive leakage.
Coefficient of friction:
Coefficient of friction f depends on the type of material of the friction pair, the type of sealing medium, the slip rate and the conditions of contact between the sliding surfaces due to construction.
For the general reasons and calculations it is necessary to use approximate coefficient of friction from 0,05 to 0,08. In the conditions of the improved lubricant, for example, at some increase in hydrodynamic pressure in a sealing gap, value of coefficient of friction decreases.
On the other hand, in a purely hydrodynamic mode of the mechanical seal and increasing the rotational speed to be expected to increase the coefficient of friction, as is the case with sleeve bearings under similar conditions.
Gap height:
For contact with the end seals theoretically strictly parallel sealing surfaces in the gap distance between them depends primarily on the roughness of these surfaces. The results are set measurements made in experimental and practical conditions have shown that when calculating the permissible leakage considering external factors necessary to take the average value of the height of the gap h less than 1 micron.
When using non-contact mechanical seal, unloaded hydrostatically or hydrodynamically, the gap height is automatically set. The height of the gap depends mainly on the shape of the gap in the radial and in the circumferential direction on the operating conditions and environment.
Roughness:
After finishing a sliding surface depending on the material has the following arithmetic average roughness Ra:
Material | Arithmetic average roughness Ra |
Tungsten carbide, ligament Ni | 0,01 micron |
Silicon carbide (SiC) | 0,04 micron |
Special chrome, alloy | 0,15 micron |
Carbon graphite | 0,10 micron |
Aluminia | 0,15 micron |
C-SiC-Si/C-SiC | 0,15 micron |
When reducing the roughness of a growing share of the load and, due to this, the bearing capacity of moving surfaces.
Sliding speed:
Sliding speed vg usually refers to average diameter of the friction ring.
For example, if the average diameter of the slip surface d m = 170 mm and shaft speed n = 4500 min-1, sliding speed will be equal to 40 m/s.
Cooling water consumption:
When calculating a consumption of the cooling water can be assumed that the cooling water heated in the heat exchanger 5K. Cooling water flow 1 l/min will provide 350 watts of heat dissipation.
Heat exchange:
To prevent overheating, seal all the power consumed by the mechanical seal must be dissipated sealing or barrier medium.
Turbulence power loss:
Influence of turbulence affects only at district speeds over 30 m/s. Turbulence power loss Pv should be considered especially in the case of special seals.
Power consumption:
The general power consumed by mechanical seal develops from:
- losses of power on friction of surfaces sliding;
- turbulent power loss due to rotating parts.
The flow rate required for the power dissipation calculated by the formula:
In certain conditions, depending on the characteristics of the installation and operation, the heat can be transferred from the product to the compacting chamber, which also must be considered in the calculation of the circulation flow.
Example of calculation:
Environment: water
The power loss due to friction sliding surfaces PR are calculated by the formula:
Calculation of leakage:
Estimated value of the leakage Q and the power loss are approximate.This statistical averages derived from numerous experiments and tests. For real actual seal leakage and power loss can be many times greater than estimated due to the presence of factors that can not be taken into account in the calculation. As can be seen from the formula, the leakage is mainly determined by the actual height of the gap, established in the course of work. This in turn depends on many factors.
Factors affecting the leakage of pumped environment:
- processing quality of sliding surfaces;
- flatness of sliding surfaces and its change as a result of deformation under heat and pressure;
- vibration level;
- operating mode of pump;
- properties of the sealing fluid;
- correctness of mechanical seal assembly.
The formula for calculating leaks for mechanical seals, loaded with external pressure: