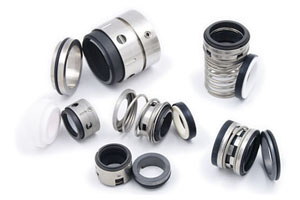
What difficulties can occur with pre-installed mechanical seals?
If you purchase a pump, mixer or other rotating equipment and do not ask the supplier to provide it with a certain mechanical seal suitable for your operating conditions and working environment, you will be very disappointed in the performance of the pre-installed mechanical seals.
If this is not done, you can sell a pump with a hydraulically unbalanced mechanical seal made of unknown materials and this will most likely lead to a leak long before the surfaces of the mechanical seal friction pairs are worn out.
In addition, the manufacturer can supply you a pump in which, as a seal for sealing the rotating parts, a stuffing box packing is used, which in turn can be too soft. As a result, this will cause problems with the sealing of working media and will adversely affect the durability of the bearings, which will lead to their premature failure.
To understand what is wrong with the pre-installed (original) mechanical seals, consider a few highlights:
- an unknown class of carbon / graphite, which may be affected by cleaners or other substances used to flush lines;
- the mechanical seal may be too porous to work at high temperatures;
- an unknown class of elastomer that has a certain temperature limit, its chemical compatibility, a short shelf life, a sensitivity to steam cleaning or processing with lubricants that can be applied to the seal during installation;
- stainless steel springs that are susceptible to stress corrosion cracking (one type of corrosion) due to chlorides;
- several springs located in the sealing medium, which can easily clog when there are solid particles;
- seals without the method of compensating for axial growth or adjusting the impeller, this is a serious problem with seals that are located opposite the shoulder on the shaft;
- seal designs that are sensitive to the diameter, tolerance and cleanliness of the surface of the shaft or sleeve;
- the recirculation and discharge line can fill the stuffing box with solids and abrasives that can interfere with the free movement of the seal and cause clogging of the filter of this line, resulting in overheating of the mechanical seal and its failure;
- rubber bellows structures, which are very sensitive to lubrication and high temperature, can start to massively refuse, and the bellows themselves burst or burst;
- structures with a single spring seal are fixed in one direction and therefore sensitive to the direction of rotation of the shaft.
Look at the picture below.
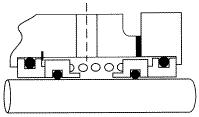
It depicts a rotating double mechanical seal such as "back to back" with a number of problems that include:
- spring elastomers that cause damage in two places on the shaft or bushing;
- structures in which the spring load on the sealing surfaces increases and decreases as the axis moves;
- on a rotating surface, solid particles are formed, as carbon wears out, causing "surface hanging" and premature failure;
- surfaces that are compressed by the pressure of the barrier liquid and decompressed if a pressure jump occurs in the system, or the pressure of the barrier liquid disappears;
- impurities and solid particles are centrifuged into the ground surfaces of the inner seal;
- If the outer seal fails or wears out, the internal seal will swell when the pressure of the barrier liquid is gone, which will make the design unsafe;
- the absence of the possibility of venting the sealing surfaces when the seal is installed in an upright position.
To avoid such problems with mechanical seals, you should avoid using pre-installed mechanical seals.
Inform your supplier that you need balanced o-rings made from the proper materials, and the material manufacturers must be identified.
To ensure a longer service life of the mechanical seal, do not disregard the following recommendations:
- inform the supplier of the operating conditions and working environment parameters in order to pick and install in the pump initially those mechanical seals that are suitable for your needs;
- ask for the installation of hydraulically balanced O-rings;
- ask for information about the sealing materials, so that you can identify them by their composition and class;
- to facilitate installation, use separating or cartridge seals;
- connect the suction return line between the front of the stuffing box and the suction side of the pump or any other low pressure point in the system.