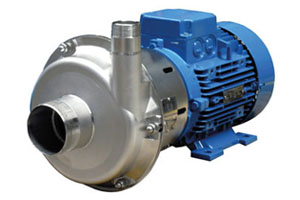
Many problems with pumping the liquid arise because some pump designs are not designed or suitable for use under the operating conditions for which they are selected. It is necessary, depending on the operating conditions, to determine the type of pump used.
Once you have determined which pumped medium you are working on, you need to consider other parameters, including: the necessary fluid or vapor pressure, the temperature and volume of the pumped medium, the solids content, corrosiveness, toxicity and sanitary standards. The correct materials are selected in accordance with the properties of the pumped medium. In the food industry, the choice of materials is particularly important, as compliance with the rules of the international regulatory bodies EHEDG, FDA and 3A is the main requirement.
The pumped medium containing solids is a common problem that occurs at different stages of the processing cycle in the food industry. Solids must be pumped without damage to the pump, or pumped, pre-grinding them. Also, it is necessary to take into account the consumption and possible errors that may occur during the addition of ingredients or increase their dosage.
Types of pumps that are most often used in the food industry:
- rotary pumps
- rotary-piston pumps
- piston pumps
- liquid-measuring pumps
- peristaltic hose pumps
- screw pumps
- membrane (diaphragmatic) pneumatic pumps
A common factor in the design of these pumps is their ability to softly pump the working fluid, even if it contains solid particles.
Rotary pumps use a gear that eliminates contact between the rotors and allows them to process non-lubricating (non-fatty) fluids, ensuring low shear and gentle handling of the liquid, thereby minimizing product breakdown. There are various designs of the rotor, including two-leaf and multi-layer. Rotary pumps are also easily cleaned in place or cleaned between each new mixing or pumping process.
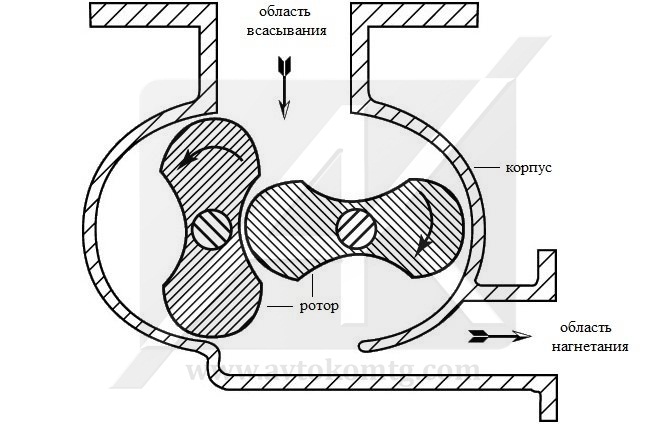
The rotary piston pump has great advantages. In this design, the pistons or impeller of the rotor are moved in annular cylinders, in the pump casing. The resulting long seal path reduces slippage and provides a smooth flow of liquid without destructive pulses or pressure peaks.
Since the rotors produce scoop, they do not compress or compact the pumped medium. This type of pump combines a very soft, noiseless, pumping action with a high suction capacity necessary to allow the drawing of thick mixtures into the pump without any separation of the ingredients.
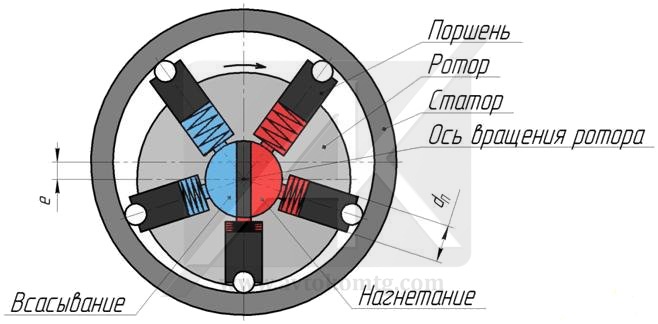
The piston pump is a completely different way of pumping the liquid, thanks to the reciprocating pistons that displace the liquid, this pump is the most suitable solution for filling and dosing lines for liquids, providing the maximum level of accuracy and stability. Factors influencing the choice of a liquid metering or metering pump, unlike other types of pumps, are usually associated with accuracy over the range of flows and with the fact that the power is not affected by pressure fluctuations during pumping.
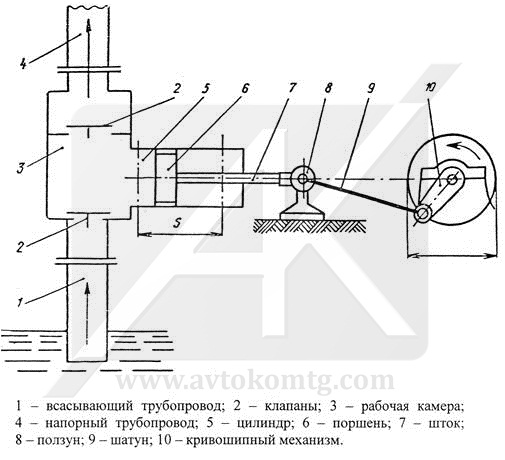
The liquid measuring pump is adapted and, thanks to its design, is ideally suited for continuous, in-phase measurement of single or multiple fluid systems at different rates. This is the only pump with two ways of adjusting the flow rate and stroke length, which can be changed independently or simultaneously for optimal performance. For example, in a process where the ingredient needs to be carefully added to the variable mainstream, the proportion can be maintained by adjusting the speed, while any adjustments necessary to maintain the quality of the product can be made by adjusting the stroke length. This means that the metering pump can be precisely tuned to the requirements of the system.
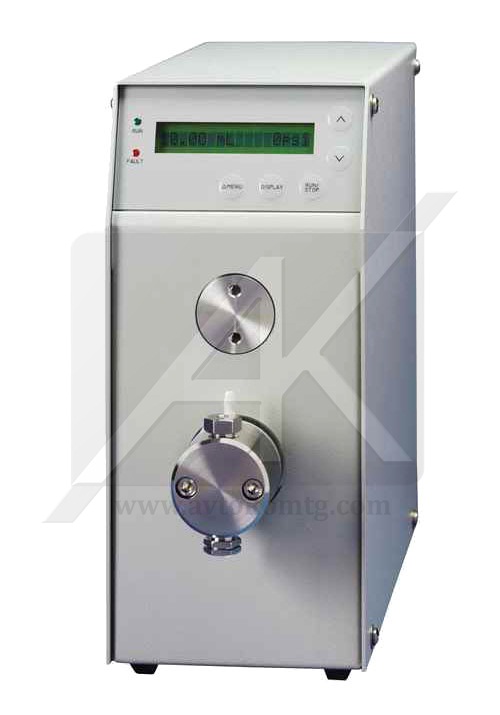
Peristaltic hose pump can also be considered for use in food production, where raw materials or ingredients must be added to the treatment system with high levels of accuracy and stability. Using the principle of moving the medium through the hose, squeezing it between the rollers or shoes at certain intervals to create a positive displacement, completely eliminating the possibility of contamination of the pumped medium. The possibilities of this pump are varied, including the possibility of introducing sensitive dense substances, dosing of flavors, seasonings and syrups. This pump provides dry running and self-priming, and also provides all the important requirements for low shear.
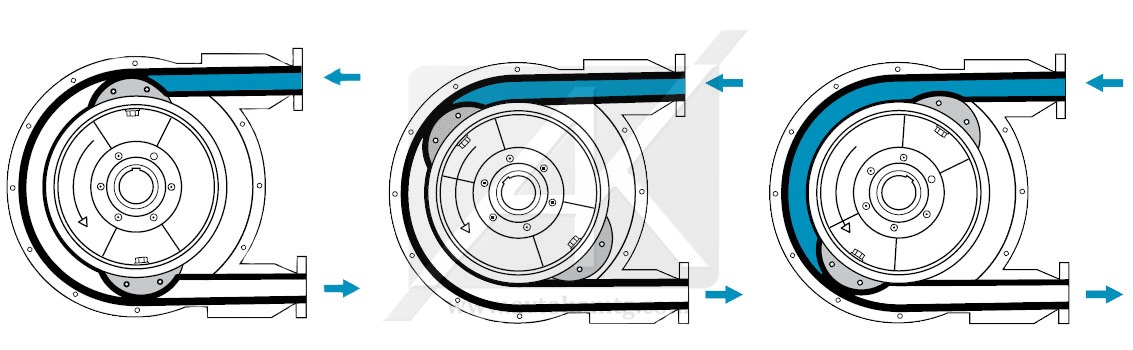
If it is necessary to move the working medium (raw materials or ingredients) at low speeds, a screw pump can be used, which also provides low shear characteristics. When using a single rotor to move fluids in a continuous flow, the performance of the screw pumps depends largely on the geometry of the rotor and the stator in which it rotates. The materials from which these two elements are made must be compared with the pumped medium with which they come in contact. To achieve the maximum life cycle, the rotor and stator must be resistant to aggressive fluids.
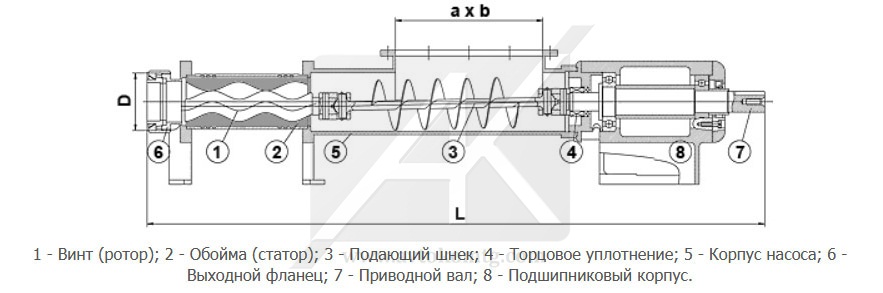
When choosing a pump for the food industry, you should also pay attention to the membrane (diaphragmatic) pneumatic pump , because there are many spheres of its use. The wide application of the pump is due to the fact that it can pump almost anything. The absence of tight fitting parts allows solids to pass through the pump without causing damage to it, while abrasive and viscous liquids can be pumped without any change in the characteristics of the pumped medium.
The diaphragm pneumatic pump uses compressed air to operate the diaphragm and draws the liquid medium into the pump chamber, and then pushes it out, so there are no rotating parts in it. In operation, the dynamic components that come into contact with the liquid are two diaphragms, which are connected together by a common shaft, two balls of the intake valve and two balls of the exhaust valve. The movement of the diaphragms with compressed air, rather than the shaft, balances and evenly distributes the load to the diaphragm, thereby eliminating mechanical stress, thereby increasing the life of the diaphragm itself.
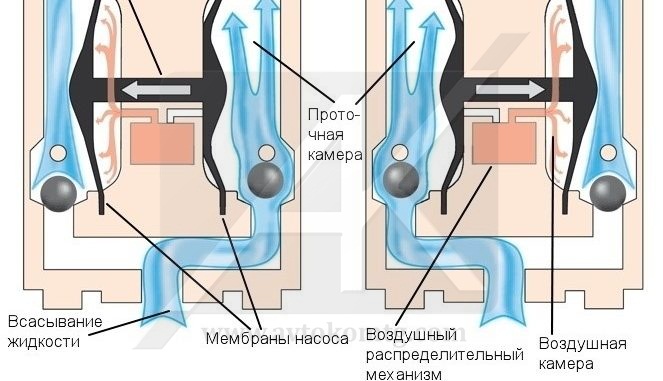
Pumps designed for pumping certain media are often more expensive, but they can compensate for additional costs in the future that usually arise during the operation of simple and inexpensive equipment. This is achieved by reducing the cost of maintenance, because A more reliable and high-quality equipment is used, which is specially designed for pumping a certain working environment, and therefore more efficiently performs its functions.
The consequences of choosing an incorrect and substandard pump are accompanied by frequent downtime, maintenance costs and repair of pumping equipment, due to the constant replacement of spare parts. In addition, costs arise due to unnecessarily expensive and complex installation, monitoring, monitoring and safety systems, which in turn create an additional item of maintenance costs. But the most dangerous thing is that the risk of getting a substandard product increases, and the threat to the life and health of the end user arises, if such a product is on sale.