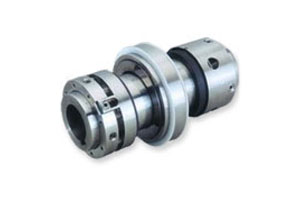
Where have we been, and where should we be going? You've been using mechanical seals for many years now. Over the years you've witnessed many design changes, but have there been any real improvements in seal performance, or is your increased seal life coming from the use of environmental controls, such as flushing, quenching and the use of jacketed stuffing boxes?
I'm going to attempt to list the most significant improvements in the basic design of mechanical seals and give you some ideas as to where the sealing industry should be spending their development dollars.
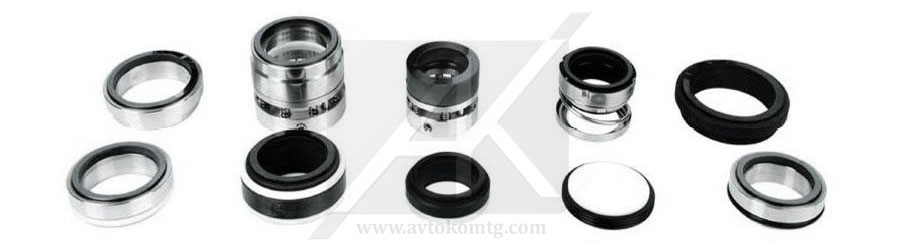
Here are some of the advancements that have been made, contributing to longer mechanical seal life:
- The general acceptance of hydraulic balanced seal designs that eliminated a major source of unwanted heat at the seal faces;
- Designs that keep the springs out of the sealing fluid;
- Stationary seal designs that reduced the problems associated with the lack of stuffing box to shaft squareness;
- The use of O-rings that reduced the problem of sliding dynamic elastomers;
- Self-aligning seal faces (Both faces spring loaded) that made the sealing of horizontally split pumps practical;
- Cartridge seal design that solved a lot of the seal failures caused by improper seal installation, shaft thermal growth and open impeller adjustment;
- Self-aligning, stationary cartridge seals;
- Unfilled carbon seal faces that eliminated most of the chemical compatibility problems we had sealing process pumps;
- A special grade of Dupont's elastomer Viton® that has a reasonable amount of water sealing capability;
- Chemraz and Kalrez. The wonder compounds of the 1970s that allowed mechanical seals to be chemically compatible with just about any fluid;
- The creation of alpha sintered silicon carbide hard faces that are not only corrosion resistant to most fluids, but also excellent conductors of heat;
- The elimination of Teflon in many original equipment seals;
- Teflon was the main contributor to shaft fretting;
- Non-fretting seal designs that eliminated the need for sleeved shafts;
- Welded metal bellows designs that eliminated the problems of elastomers in cryogenic and non-petroleum, high heat applications;
- Split seal designs that eliminated the last reason for using packing in pumps;
- Finite element analysis techniques that allow us to design small cross-section seals with high-pressure capability;
- The use of suction recirculation piping along with an oversized stuffing box to eliminate most of the problems associated with the sealing of slurries.
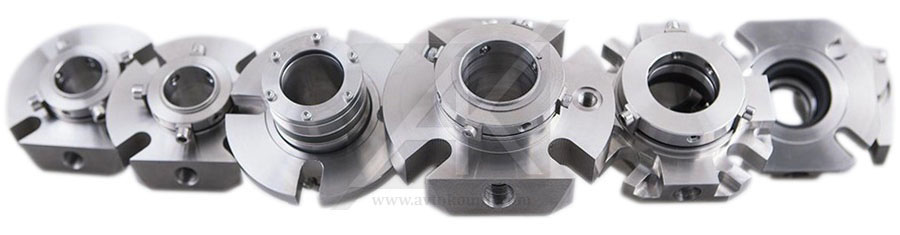
What will you need in future years?
- The elimination of elastomers in process seals, not only because of elastomer temperature limits, but the more serious problem of chemical compatibility with both product and flushing fluids. Someone has to pick the correct elastomer and there is always room for error;
- Seal designs that can take excessive axial movement without changing their face load;
- The elimination of barrier or buffer fluid between dual mechanical seals. Present gas designs are not filling this need;
- Temperature control in the stuffing box area without the use of water or steam. In many applications the fluid in the stuffing box must be kept within certain temperature limits to prevent it from changing into a sold or a gas;
- Instrumentation to predict pump cavitation, excessive shaft deflection, high heat, etc. that shorten seal life;
- Reliable non-stick seal surfaces to prevent solids from adhering to the sliding seal components.
What are the reasons for the increased seal life we're experiencing now?
- A better educated consumer. Many of the mechanics and engineers have received specific seal and pump training.;
- The wide use of cartridge seals that has made installation easier and less error prone;
- The oversized stuffing box;
- Suction recirculation piping that has eliminated many of the problems associated with the sealing of slurries;
- The demise of unbalanced seal designs;
- Better motor/ pump alignment ever since the popularity of laser aligning and the increasing use of C & D frame adapters;
- The more common use of environmental controls in the stuffing box area;
- Finite element analysis to prevent seal component distortion problems;
- Better seal materials.