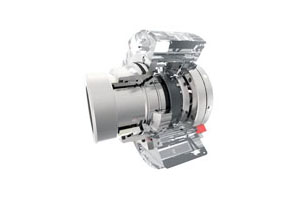
Kroma LTD, working in the sealing industry, has always believed that this industry is different from the others. It has a lot of features that define your company in every way. These features affect your product range, customer approach, workflow, the structure of your organization and many other factors.
However, the success story of Kroma LTD is also related to the difficulties faced by many developing companies. One of the most important problems is competition with larger companies. The problems that we faced in all small companies are the same: lack of resources, lack of a proven brand, not the possibility of large-scale production with low costs, etc.
Working in the sealing industry, we are constantly competing with such large companies as Eagle Burgmann, John Crane, Chesterton, Flowserve, etc.
As our experience shows, the key to successful competition with large companies is knowledge.
The success story of Kroma LTD began in the oil and gas industry. At the local oil refinery, there were problems with seals on pumps operating in very difficult conditions. It was a great opportunity for a small company, such as ours to declare themselves. We came to the matter with all responsibility. Our engineers have developed special seals for these pumping units.
Our biggest advantage is the individual approach to the client.
It is an individual approach that has played a decisive role for our customer. We acted flexibly, were well prepared, responded promptly to the wishes of the customer, effectively applying our knowledge. Due to the fact that we worked closely with our customer, the mechanical seal developed by us, in terms of its performance characteristics, and as it turned out later, the service life - had no analogues in the market for pump seals.
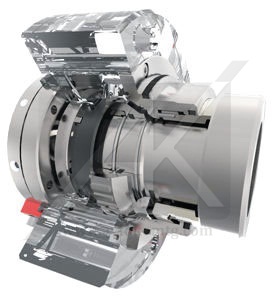
The development of this unique seal became possible only due to the investments of the customer, to which we offered an individual approach and a personal configuration of the seals.
While other well-known large companies were not so meticulous and offered standard, inefficient solutions that they had in the catalog.
Also many other types of vapors and gases can easily be adsorbed by carbon graphite, and in some cases, inorganic compounds can be added to carbon graphite if the absorbed gases are absent or in deficit. This is one of the solutions to the problem of the distribution of hot, dry air in the seal. Carbon graphing (conversion of bound carbon, into free graphite, by heating to 4000 degrees Fahrenheit or 2200 degrees Celsius) is also another way of self-lubricating.
Such customers should be the top priority for sales managers, they should find the key companies that need to make changes to the product, in this case, the seal. It is important to establish contact with your client. It is necessary to fully understand the essence of his problem and try to solve it. You need to be more flexible than competitors, to study the technological process of your client, and adapt the new solution to his needs.
After testing our new mechanical seal, it was selected as the best seal in accordance with the pump conditions. Thanks to our development, we were able to make a worthy competition for the leaders in this industry.
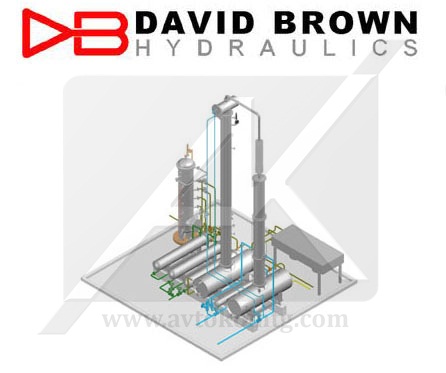
Technical data and operating conditions of the plant:
Purpose: visbreaking pump.
Device: David Brown type 3x4x9B pump - MSD 8 st.
- Speed (min-1): 2960
- Fluid: Atm. Residue
- Temperature: 93 (140°C)
- S.G. at P.T.: 0.88 (0.85)
- Suction pressure (barg): 1,37
- Discharge pressure (barg): 38,54
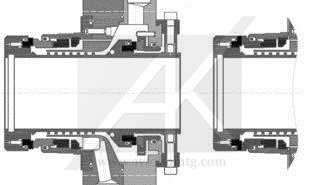
Previously, our client used on this unit a single seal proposed by one of the large companies. The seal was practically unsuitable for use. The results of using this single seal in the pump, as presented by the maintenance technician, were as follows:
- an average of 7 pump failures per year;
- more than 90% of failures were caused by failure of the mechanical seal.
The seal developed by Kroma LTD was a dual cartridge seal in tandem design with barrier fluid and API 53A, with monolithic sealing surfaces (tungsten carbide / self-baked silicon carbide). This seal is ideally suited for the harsh operating conditions inherent in this installation. Our compaction was more balanced, with an optimal flow of barrier liquid, which allows us to more effectively regulate the thermal properties.
After installing our seal, the performance of the pumps was as follows:
- since the installation of the new seal (August 2015), the pump has operated smoothly, to the present day (October 2017);
- the ecological aspect of the plant has improved;
- the reliability of the system has significantly improved;
- significantly reduced maintenance costs.